About us
Our Process
BlackMilk was born right here in Brisbane, Australia. It's where we built up our expertise on making all the weird and wonderful things we are known for, which means there are two things we’re really good at: making shiny gear, and dealing with subtropical spiders
Our local manufacturing teams still work day in day out at BMHQ, bringing magic to life through printers, laser cutters and sewing machines. Here's a snapshot of our local manufacturing process:
Fabric Warehouse & Cutting
We use roughly 80 different types of fabric to make your amazing clothes – so, as you can imagine, we hold a LOT of fabric on site. Our Warehouse team receives up to 400 rolls of fabric each month from our various suppliers. Using their amazing Tetris skills (and a forklift), they organise the fabrics from newest to oldest and complete regular stocktake to keep track of how much we have on hand of any specific fabric.
The cutting process takes precision. We have this really cool machine that is programmed to cut out each panel of fabric that makes up your clothes. Our Cutting team programs the machine and makes sure everything runs smoothly.
In our cutting room, our talented team creates markers for the cut process. The marking involves arranging the various pattern pieces on a computer screen to make sure we use every inch of fabric possible – no waste here! Working together, our Marker Maker and Spread Operator use an automatic fabric spreader to lay out the fabric, ensuring only the fabric that is required is used in the lay for cutting.
Once the fabric lay is completed, our Cut Operator programs the markers into the cut machine for automated cutting using large, specialised machinery. Items are then bundled and prepared for printing or sewing.
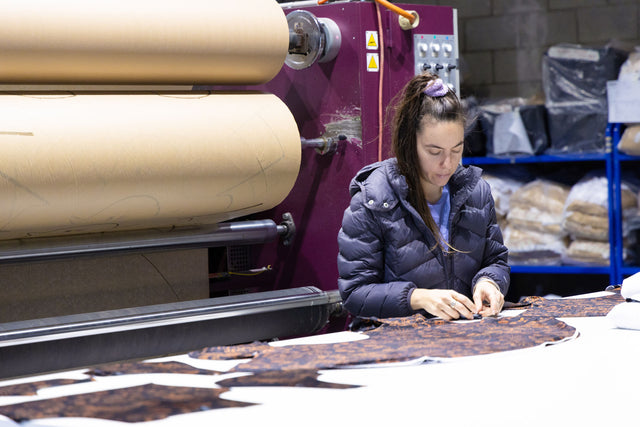
Printing
We call our printing team BMS (BlackMilk Sublimation). These guys get the epic prints from Graphics out of the computer thing-ma-bob and onto your gear!
Our BlackMilk prints are something that we are super passionate about. We have a history of creating prints that are unique and bold. We don’t just believe in wearing your heart on your sleeve – we think that’s a total wardrobe kind of deal.
The majority of our prints are achieved through the sublimation process. Haven't heard of it? Sublimation is a fancy name for the process of turning a solid into a gas using high heat.
Our print team works closely with the graphic design team, taking their artwork and printing it onto giant rolls of paper. Next, it’s taken through the heat press.
While the paper is running through the heat press, one of the team members is at the helm, laying out the cut fabric panels onto the moving paper. We find printing onto pre-cut fabric panels reduces ink usage and makes the process more efficient – but you've gotta be quick, this paper waits for no human!
The heat causes the ink on the paper to turn into a gas which is absorbed by the fabric. When it comes out the other side, the now boldly-printed fabric is removed from the paper and voila – you’ve got yourself some BlackMilk awesomeness!
The printed panels are now ready to be neatly stacked, counted and checked for any slight printing misses or faults, before we send them down to our sewing team who put them all together for you!
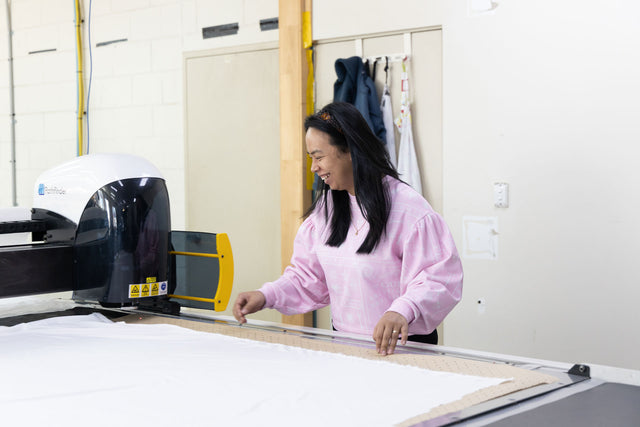
Sewing
Once the cut and printed panels arrive at sewing, they are given to our highly-talented sewing team together with our tech packs to assemble. With so many different styles, shapes and fabric types, our Sewing Machinists are kept on their toes! It is important that our team is multi-skilled across fabric types and machines.
Once the cut and printed panels arrive at sewing, they are given to our highly-talented sewing team together with our tech packs to assemble.
Sewing Machinists work in smaller teams or modules and each person in the team completes one stage of the assembly process. Depending on the piece, this could include overlocking the panels together, cover seaming to finish the garment edges or plain sewing pockets onto garments (‘cos we know you love pockets!).
One product that we are super proud of is our Inside Out Dress – a truly unique BlackMilk design, and one that took a LOT of trial and error to make into a thing! To make these dresses wearable on both sides without inside seams, our talented Machinists use a special machine called a flatlocker. This is a little like an overlocker, but instead of the seam being raised on the inside of the product, the seam is completely flat. Magic!
Once all of the stages of assembly have been completed, the final product is passed on to our Quality Control Team.

Warehouse
Once your gear is ready to go, it gets stored in the Warehouse ready to be picked and packed when you order. These guys are known as our Packing Ninjas for a reason – they handle a huge volume of orders. Their current record is 1144 orders dispatched in a single work day. That’s a LOT of shiny goodies.
Once an order is received, these are the ninjas who jump into action to pick out all the things that you want on your bod, package and label them up and load them up for collection from our delivery partners!

Quality
Our Sewing and Quality Control teams are proud of their work and for good reason. The quality of our gear is super important to us, so our talented senior sewers conduct product quality checks at regular intervals throughout the day and support their teams with advice and guidance. To maintain our high standards, our quality checks are recorded daily.
Once the garments are sewn, they are taken to the Quality Control room, where they undergo a full visual quality inspection (and where you can hear the best music pumping). Our eagle-eyed and highly experienced QC-ers can spot the tiniest detail and thoroughly review each garment.
At the final stage, the garments are tagged, barcoded, folded and packaged by hand. Each person responsible for folding and bagging gives each garment a second visual look over before the final products are transferred into the warehouse – ready for delivery!
